安くて早いし1個からOK!
光造形とは
光造形とは、紫外線照射で硬化する特殊材料を用いた積層方式のラピッド造形工法の一つです。
切削加工に比べ工期が短く、また安価なのが一般的です。(ただし、用いる材料が特殊材であることから、製品サイズが大きかったり個数が多かったりすると、工期や価格も高くなる場合があります)
切削加工ほどではありませんが精度も良く、真空注型用のマスターとしても光造形品はよく利用されています。
光造形品にはサポートや積層目が残るので、基本的には造形後に仕上げ作業(ペーパー磨き)を行い、さらにサフェーサもしくはクリアコートで塗装します。
ある程度の強度はありますが、力を掛けると積層方向に割れやすい(壊れやすい)ので注意が必要です。肉厚の薄いツメ形状やヒンジ形状など、実際に力を加えたり、曲げたりする用途のモデルには不向きと思われます。製品に力があまり掛からない形状確認用としての試作品や、人の手に触れにくい展示品などには適しています。
吸湿性があり、熱に弱いという弱点を持ちます。メッキ処理は不可ですが、塗装や染色は可能です。
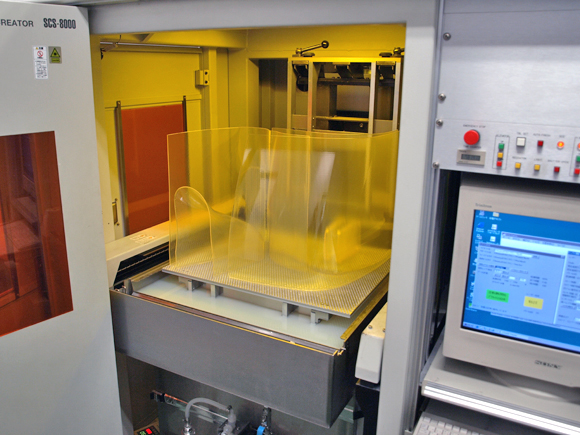
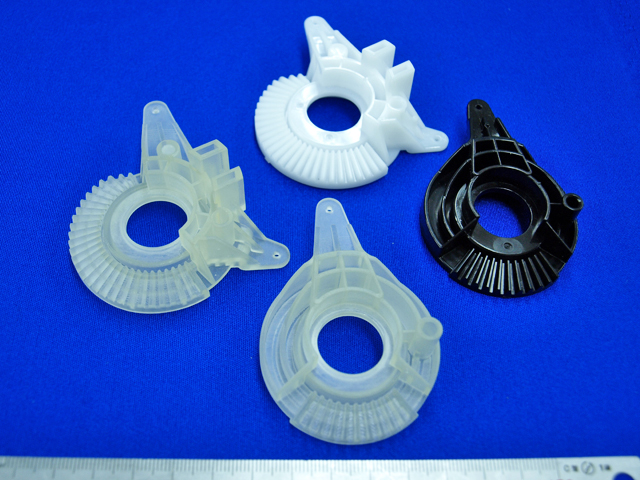
通常工期 | 手の平サイズで3~6営業日 |
寸法公差 | 中級~粗級 |
主な材料 | 紫外線硬化エポキシ樹脂 |
取扱材料 | SCR735(ABS相当) SCR737(強靭性) TSR821(強靭性) |
工法・概要 | 紫外線レーザーを照射することで硬化するエポキシ系樹脂を、0.1mmの厚みで重ねて、造形を行う方法 |
加工工程 | プログラミング→光造形→荒仕上(サポート除去)→本仕上げ(外観面の積層除去)→コーティング(塗装) |
マシンテーブルサイズ | 580×480×490 mm |
光造形の材料物性
光造形の補足事項
字の通り「層を積み重ねる」方法です。1層を描画(硬化)しては重ね・・・を繰り返して造形します。1層あたりの厚みを積層ピッチといい、積層ピッチが小さいほど外観が滑らかに造形できますが、一方で重ねる層の量が増えるので加工時間が増えてしまいます。
積層方式では必ず発生するものです。光造形の通常の積層ピッチは0.1mmです。一般的なコピー用紙の厚みも0.1mmなのですが、ちょうどコピー用紙を数十枚重ねた際の側面のガタガタの様な形状が、光造形品の側面にも出てきます。これを積層目といいます。この積層目を除去する場合はそれなりの手間と時間を要し、この作業を本仕上げといいます。荒仕上まででしたら、かなりコストを抑えられます。本仕上げは、その程度によっては価格も上がります。
荒仕上とはサポート除去までの仕上げです。本仕上げでは造形物の外観面の積層目を除去します。ただし、形状によっては積層目の完全除去ができない場合があります(磨くことが物理的に難しい箇所など)。
丁寧な仕上げが好評です
光造形品をマスターに用いる場合や、造形後に塗装など意匠処理をする場合は、意匠面を磨いて仕上げる必要があります。
当社の造形品は「仕上がりが綺麗」「仕上げがうまい」と多方面のお客様よりご好評いただいており、当社の特長として自負しております。
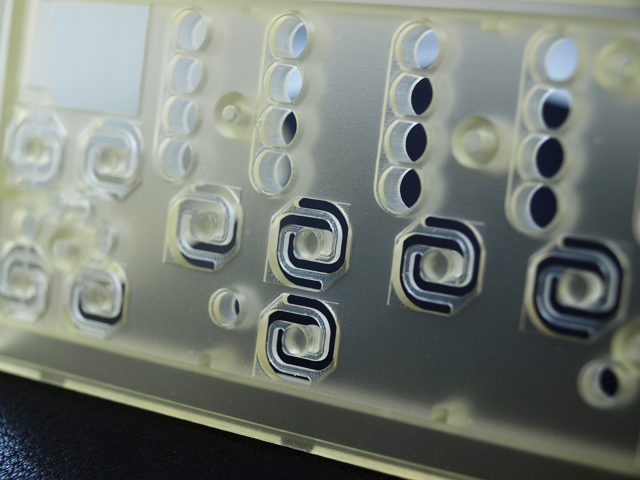
光造形のメリットと注意点
光造形のメリット
- 積層方式のため、アンダーカット形状も一体加工が可能
- 切削加工で生じる刃物R残りがない
- 切削加工や他の造形に比べ、高速で安価
※肉厚や高さがあるものなど、形状によっては切削加工より高価になることがあります。
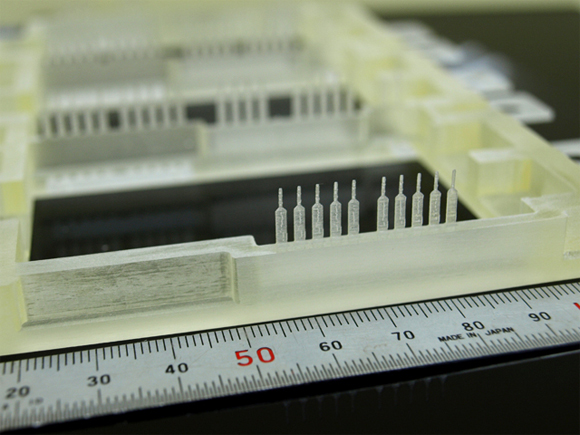
光造形の注意点
- 積層方式のため、等高線の様な模様ができる(積層目)
- サポートという支持形状(余剰形状)ができる(サポート痕)
- 材料としてはもろく、衝撃を受けると壊れやすい
- 0.3mm以下の形状は造形できない
- 造形品の中に気泡が入ることがある
※積層目・サポート痕は磨き仕上げで、ある程度の除去が可能
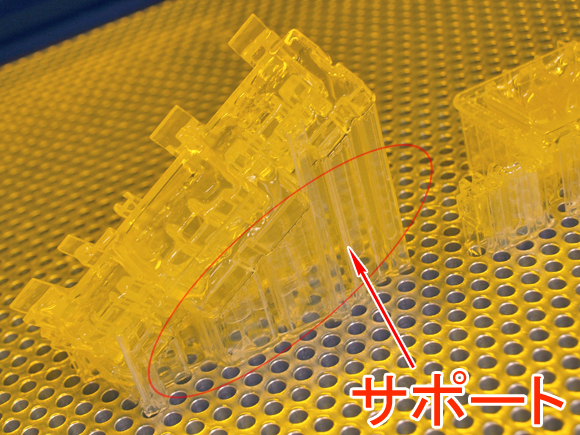
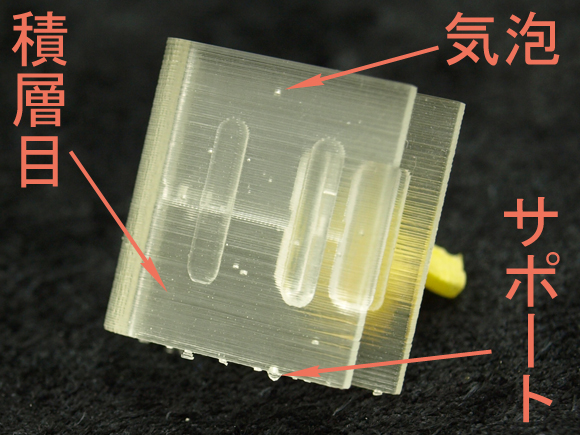
光造形の加工の流れ
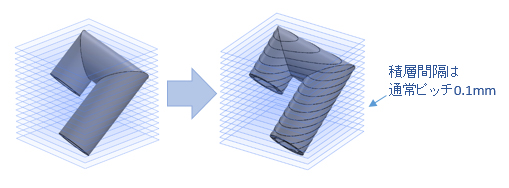
※イラストは分かりやすいように、積層間隔をかなり大きめに表現しています。通常の積層間隔はピッチ0.1mmです。
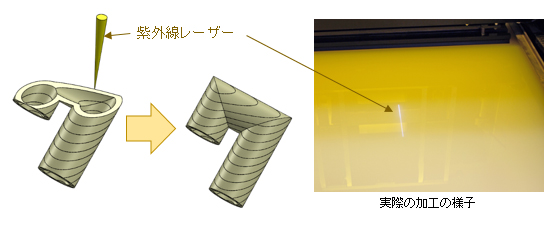
※一層毎に紫外線レーザーで液状材料を硬化させていきます。一層が硬化したら、テーブルが0.1mm下がります。これを繰り返します。
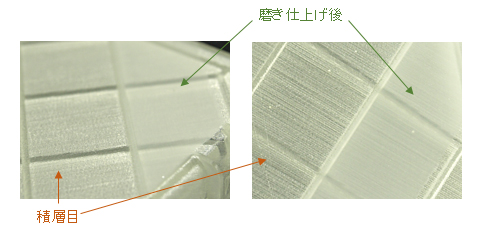
※左右の写真は同じ箇所を撮影しています。磨き後もうっすら線が見えますが、これは裏面の積層目です。
光造形品の例
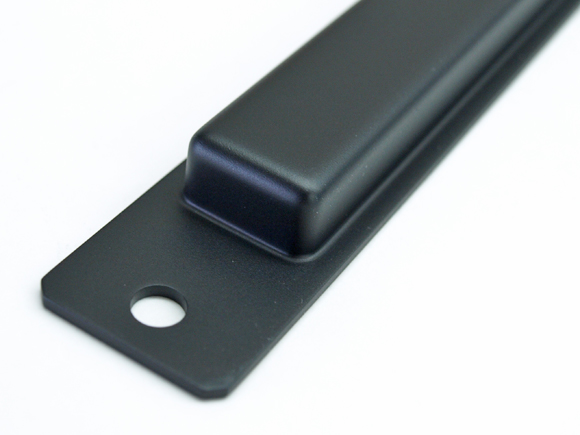
光造形品を磨き仕上げし、その上から黒塗装を施しています。

赤丸内は隙間が小さすぎたため磨き仕上げが出来なかった箇所です。磨けていないため、光造形の積層目が出ています。ただし、赤丸内は意匠面ではないため、この仕上げ具合でもOKでした。
光造形でバスバーや端子を表現しています。 染色 サフェーサー仕上げ 光造形品(500×80×40)
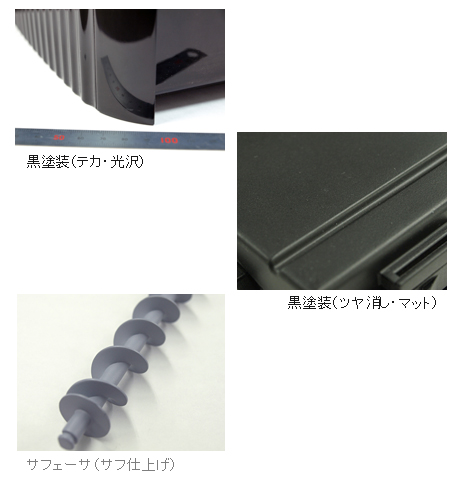