真空注型/シリコンゴム加工
真空注型は、同じ形状のモデル(部品)を複数個、小ロットで生産することに最適な方法です。
金型を起工し成形する工程に比べ、短納期・低コストで仕上がります(その反面、金型成形より寸法安定性・ロット数において劣ります。また、材料が特定されます)
※形状が非常に大きいものや、複雑な形状のものは、注型が難しい場合がございます。
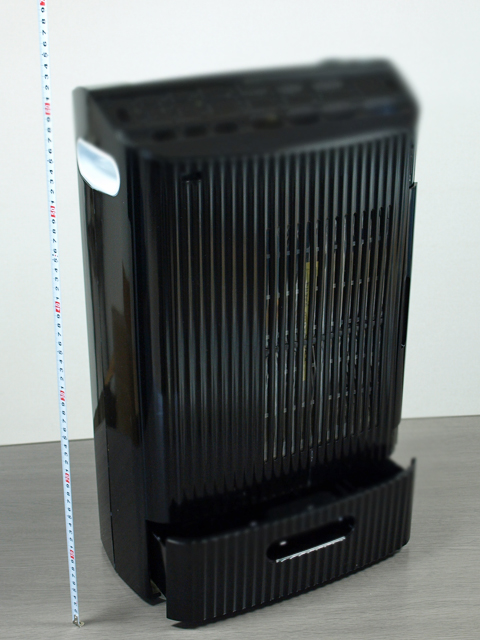
光造形で製作、艶仕上げ、塗装
(H600×W360×D220)
真空注型とは
ゴム型 | 形状を複製(転写)する試作工法 |
プラスチック型 | シリコンゴム製品を作る際の試作工法 |
真空注型は大きく2つに分けられます。
シリコンゴムを用いたゴム型を用いる注型と、樹脂を彫り込んだプラスチック型を用いる注型です。通常、真空注型と言われれば前者の場合が多いです(ゴム型を用いた注型方法はコチラ)。マスターの形状を複製する試作工法です。一方の後者は、シリコンゴム製品を作る際にシリコンゴム型では作れないので、プラスチック型を用います。プラスチック型は金型の樹脂版のイメージで、主にマシニングセンターで製作します。
いずれの場合も、製品材料には二液硬化性樹脂(主剤と硬化剤の2つの液剤を混ぜ合わせると化学反応で固まる材料)を用います。材料の硬化には少し時間がかかります。硬化してしまう前に、ゴム型もしくはプラスチック型に流し込みます。これを注型と言います。
また、2つの液剤を混ぜ合わせる際には気泡が入ってしまいます。気泡が入ったまま材料が硬化すると、ポツポツ穴が開いたような表面になったり、強度に悪影響を及ぼしたりします。そのため、注型作業を真空中で行います(真空中であれば、気泡が材料から抜けていきます)。
真空中で行う注型 → 真空注型 です。
真空注型でよくいただくご質問
- ABSで真空注型できますか?
-
ABSではできません(PCやアクリル、PPなどの場合も同様です)
真空注型で用いる材料は「ウレタン」「エポキシ」「シリコン」で、いずれも二液硬化性樹脂に限られます。ただし、真空注型用の材料に「ABS相当」「PP相当」など、○○相当としていくつかのグレードが存在ます。
- 真空注型の精度ってどれくらい?
-
マスターおよびゴム型は加工環境・使用環境の影響(温度・湿度)を受けやすいため、精度は「中級~粗級」でお考えください。成形品や切削品などに求める精度(精級)を、真空注型には求められません。
精度目安 精級 中級 粗級 0.5-3.0 ±0.05 ±0.1 ±0.2 3.0-6.0 ±0.05 ±0.1 ±0.3 6.0-30 ±0.1 ±0.2 ±0.5 30-120 ±0.15 ±0.3 ±0.8 ※精度の表は「精級~粗級」の感覚値をご覧いただくものであり、寸法公差を保証する内容ではございません。
※表は「JIS B 0405:1991」より一部抜粋
- 真空注型って何がいいのですか?
-
主にはコストメリットだと思います。
数量が5~20個ぐらいで、精度はそれほど求められず、とりあえず形状・製品が欲しい場合は、真空注型での製作をオススメしております。大きさ・形状にもよりますが、切削加工で同量を加工するより、真空注型の方が安くなることが多いです。数量が数十個~100個以上になると、金型+射出成形の方にコストメリットの軍配が上がるかもしれません。
【目安】
1個から数個なら → 切削加工
数個から20個まで → 真空注型
数十個、100個以上 → 射出成形※大きさや形状、試作品の用途によって向き不向きがございます。工法はご相談下さい。
インサート注型・着色注型
インサート注型ができます
試作成形と同様に、精密端子やバスバーなど金属・板金部品のインサート注型が可能です。また、インサート部品の手配も当社にて承ることができます。
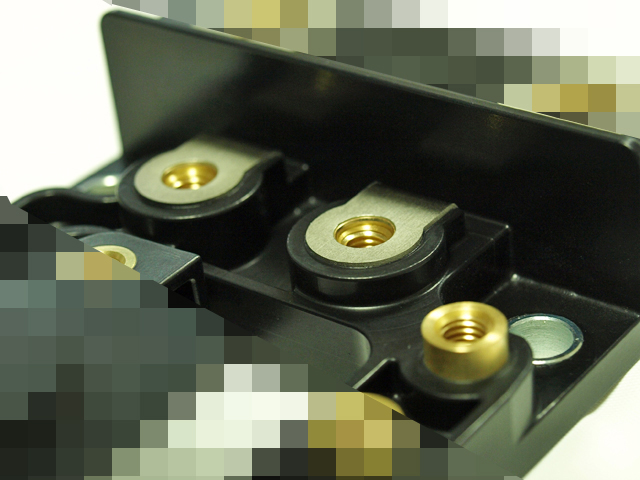
着色注型、艶仕上げ(テカ仕上げ)
材料に調色・色付けをし注型を行う着色注型も可能です。
また、マスターを磨き上げ、注型品に艶(テカ)を出すことも可能です。
光造形のマスターに艶仕上げ・塗装することで、注型品に艶(テカ)が出ます 注型品(白着色、艶仕上げ) 注型品(白着色、艶仕上げ)
真空注型の工程(注型手順・ゴム型を用いる場合)
まず形状の元となるマスターモデルを製作し、そのマスターをシリコンゴムで覆います。
次に、シリコンゴムを分割しマスターを取り出します。ゴムだけの状態をゴム型と呼びます。
分割したゴム型をマスターの無い状態で密着させ、マスターのあった空間に注型材料を流し込みます。
注型材料が十分に硬化したら、ゴム型を再度分割し、硬化した製品(注型品)を取り出します。
この方法を繰り返し、マスターモデルの形状を複製します。
※上記は注型材料がウレタン・エポキシの場合です。シリコンの場合はアクリル型を起工します。
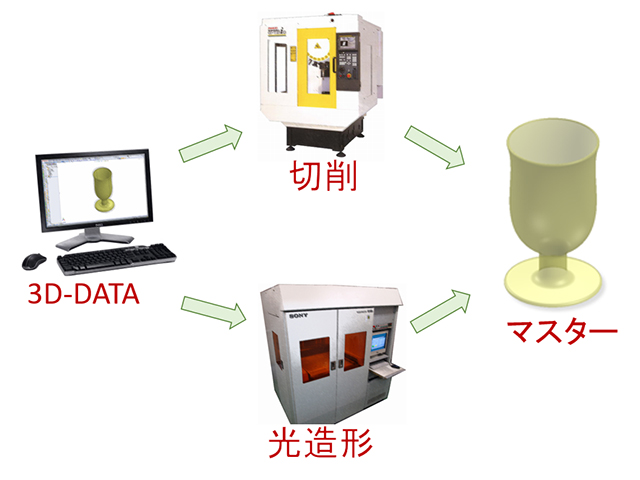
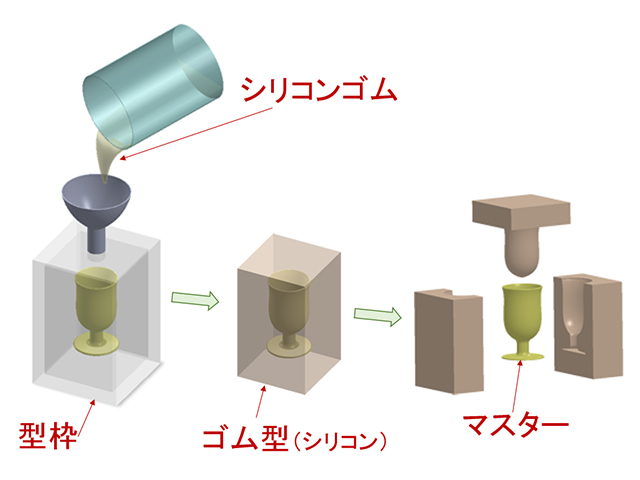
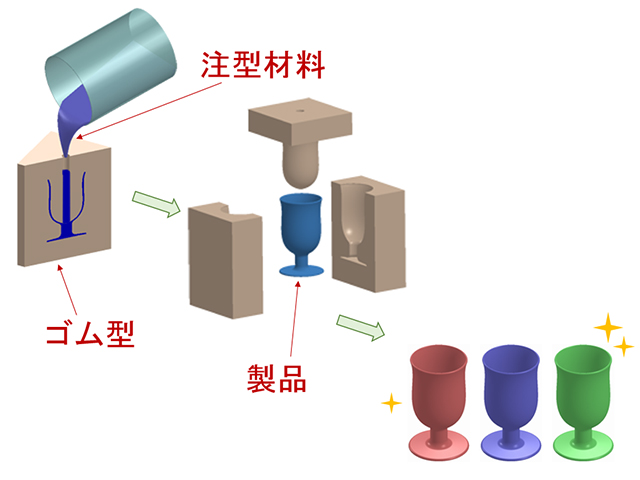
マスターモデルは光造形もしくは切削加工により製作
光造形では複雑な形状であっても、切削加工に比べ短時間・低コストで製作できます(その反面、寸法安定性が劣ります)。
切削加工では大きさ・形状によっては加工時間・コストがかかりますが、寸法公差が確かです。
具体的なマスター製作方法は当社にご相談ください。形状・コスト・納期より検討・提案致します。
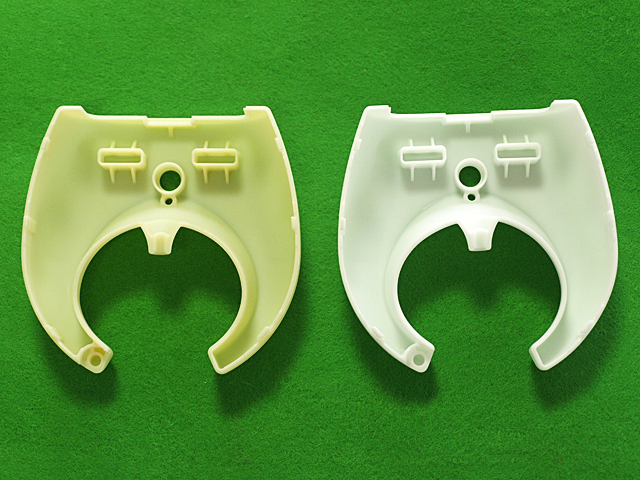
1つのゴム型で注型可能なロット数は15~20個
サイズ・形状に大きく依存しますが、寸法・品質を考慮すると、通常1つのゴム型で注型可能なロット数は15~20個です。
また、時間経過に伴い寸法が安定しにくい(湿気により膨張)光造形のマスターは、起工できるゴム型の数に限りがあります。
つまり、ロット数が多くなる場合、製作するマスター数量も起工するゴム型数量も多くなります。
注型用の樹脂材料はウレタン・エポキシ・シリコン
当社で取り扱い可能な注型材料はウレタン・エポキシ・シリコンの二液硬化性樹脂です。
材料名 | ウレタン | エポキシ | シリコン |
グレード(硬度) | ABSグレード PPグレード アクリルグレード ゴム(A50~A90) | ABSグレード | ゴム(A40~A60) |
耐熱温度 | ベーシック 80~90℃ 耐熱グレード 110~120℃ | 70~80℃ | 200℃ |
カラー | ベージュ・黒・乳白・透明 ※色付け・着色可能 | ベージュ・黒 ※色付け・着色可能 | 乳白 ※色付け・着色可能 |
※本表の数値はあくまで参考値であり、規定値ではありません。
※製品の物性は形状や成形条件によって異なります。
※材料指定がない場合、当社にて形状に適した材料を選定することがあります。
※耐熱グレードには着色できない場合があります。
意匠仕上げ・表面処理もお任せください
これまで、自動車分野・OA機器分野・弱電分野における試作モデル・試作部品の成形・納入実績がございます。
注型品への塗装・印刷(シルクスクリーン・インスタントレタリング)・レーザーマーキングも、ぜひお任せください。
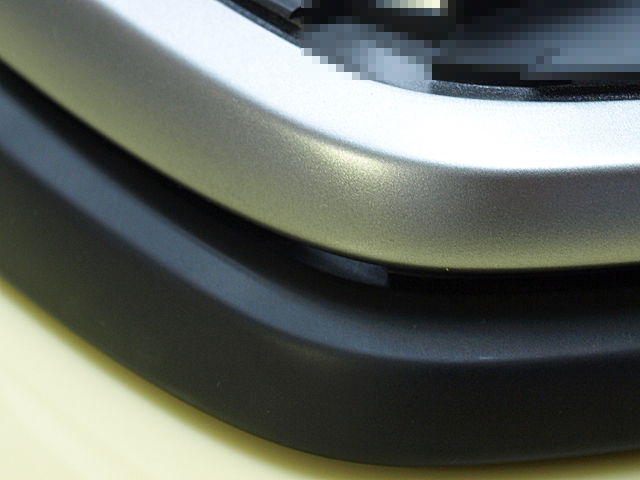
下:塗装前、上:塗装後(注型品・シルバー)
真空注型品
マスター(左・切削+磨き仕上)と 注型品(白着色) 高精密光造形にてマスターを用意し、注型 ゴム注型品(ウレタン、着色:黒) シリコンゴム(真空注型) 注型品(白着色)200×200。 シルク印刷・アッセン含む